Have you ever thought about why yarn count is crucial in the textile industry? What does this technical term really mean? Yarn count is frequently mentioned, but do we really grasp its influence on fabric quality and characteristics? Let’s explore the realm of yarn count and uncover why it plays a critical role in textile production.
Key Takeaways:
- Yarn count plays a vital role in determining the thickness, fineness, and overall quality of a yarn.
- Different yarn counts have various applications and significantly impact fabric weight, texture, and appearance.
- Understanding and selecting the appropriate yarn count is essential for achieving desired fabric properties and aesthetics.
- Fiber type, end-use requirements, fabric structure, and aesthetic preferences are factors that influence yarn count selection.
- Consistency in yarn count is crucial for fabric production.
What is Yarn Count and How is it Measured?
In the world of textiles, yarn count is a crucial measure that determines the fineness or thickness of a yarn. It is an essential aspect of producing high-quality fabrics and plays a significant role in various textile applications.
Yarn count can be measured using different systems, namely the direct system and the indirect system. Let’s explore each of these systems in more detail:
The Direct System:
In the direct system, yarn count is determined by calculating the weight of a specific length of yarn. This system includes measurements such as tex, decitex, and denier. Tex is commonly used in industrial settings and represents the weight in grams per 1000 meters of yarn. Decitex is similar to tex but represents the weight in decigrams per 10,000 meters. Denier, on the other hand, is a measurement used primarily for synthetic fibers and represents the weight in grams per 9,000 meters.
The Indirect System:
The indirect system measures yarn count by determining the length of yarn required to achieve a specific weight. This system includes measurements like Ne (English Cotton Count) and Nm (Metric Count). Ne represents the number of hanks of yarn per pound, where one hank is equal to 840 yards. Nm, on the other hand, represents the number of hanks of yarn per kilogram.
By using these standardized systems, textile manufacturers can ensure consistency and accuracy in measuring yarn count. This allows them to produce fabrics with the desired characteristics and meet the requirements of various end products.
To provide a visual representation, here’s an image depicting the different yarn count measurement systems:
https://www.youtube.com/watch?v=0sYiQiMsZhc
Understanding yarn count and its measurement methods is crucial for textile professionals striving to produce fabrics of the highest quality. With these systems in place, manufacturers can confidently select the appropriate yarn count for their specific applications and achieve the desired fabric properties.
The Significance of Yarn Count in Fabric Characteristics
Yarn count is a crucial factor that influences the characteristics of the final fabric. It plays a vital role in determining the weight, texture, and appearance of the fabric. The choice of yarn count can result in fabrics with distinct qualities that are suitable for various end-use applications.
Finer yarns, which have a higher yarn count, tend to create lighter and more delicate fabrics. These fabrics are often preferred for applications where lightweight and breathable materials are desirable. On the other hand, thicker yarns, with a lower yarn count, contribute to heavier and more robust textiles. These fabrics are suitable for applications that require durability and strength, such as upholstery or heavy-duty clothing.
Yarn count also directly influences the texture of the fabric. Finer yarns create a smoother and more refined texture, while coarser yarns result in a more textured and pronounced surface. The choice of yarn count can enhance the tactile experience and overall feel of the fabric.
“The choice of yarn count can result in fabrics with distinct qualities that are suitable for various end-use applications.”
In addition to weight and texture, yarn count significantly impacts the visual appearance of the fabric. Finer yarns often create fabric with a more detailed and intricate appearance, while coarser yarns can result in a more rugged and rustic look. Designers can leverage the characteristics of different yarn counts to achieve specific visual effects or match the aesthetic requirements of their designs.
Overall, yarn count plays a critical role in determining the characteristics of the fabric. It influences the weight, texture, and appearance, allowing manufacturers and designers to create fabrics with distinct qualities tailored to specific end-use applications.

Factors Influencing Yarn Count Selection
When selecting the appropriate yarn count for a fabric, several factors come into play. We carefully consider these factors to ensure that the yarn count aligns with the specific needs of the project. Understanding these influences allows us to create fabrics that meet the highest standards of quality and performance.
Fiber Type and Yarn Count: The type of fiber used in the fabric significantly impacts the optimal yarn count. Different fibers possess distinct characteristics that influence their thickness and strength. For example, a delicate fiber like silk may require a finer yarn count, while a robust fiber like wool may necessitate a coarser count. By taking fiber type into account, we can choose the most suitable yarn count for each specific material.
End-Use Requirements and Yarn Count: The intended purpose of the fabric also plays a vital role in determining the appropriate yarn count. Different end-use requirements dictate specific characteristics that the fabric must possess. For instance, fabrics intended for heavy-duty applications, such as upholstery, may benefit from a coarser yarn count to enhance durability. On the other hand, delicate fabrics like lingerie may call for a finer yarn count to achieve a luxurious feel.
Fabric Structure and Yarn Count: The structure of the fabric, such as the weave or knit pattern, is another influential factor in yarn count selection. Different fabric structures have unique requirements in terms of yarn count to achieve specific properties. For example, a tightly woven fabric may require a finer yarn count to ensure a smooth and uniform surface, while a loose knit fabric may benefit from a coarser yarn count for added bulkiness.
Aesthetic Preferences and Yarn Count: Aesthetic considerations also come into play when selecting the yarn count for a fabric. Designers often have specific visual and tactile effects in mind when creating a fabric. They may choose a finer yarn count for a delicate and lightweight appearance or a coarser yarn count for a textured and robust look. By incorporating aesthetic preferences into the yarn count selection process, we can bring the designer’s vision to life.
By carefully considering these factors, we are able to make informed decisions when selecting the yarn count for fabrics. Our aim is to create textiles that not only meet functional requirements but also embody the desired aesthetic and performance characteristics. Yarn count plays a vital role in achieving these goals, ensuring that the fabric we produce exceeds expectations.
Yarn Count and Its Impact on Yarn Cost
When it comes to yarn production, the yarn count plays a significant role in determining the cost. The yarn count refers to the fineness or thickness of the yarn, and it can influence the overall production expenses.
Finer yarns, which have a higher count, often require more intricate spinning processes. These processes, such as higher twist levels, can increase production costs as they involve more time and resources. On the other hand, coarser yarns with a lower count may be more economical to produce due to their simpler spinning processes.
Manufacturers need to consider the cost of yarn as an essential factor when selecting the yarn count. The production cost of finer yarns can be higher due to the intricate spinning processes involved, while coarser yarns may offer a more cost-effective option.
Understanding the relationship between yarn count and production cost is crucial for making informed decisions and optimizing the manufacturing process. By carefully considering the cost implications of different yarn counts, manufacturers can achieve their desired fabric quality while managing their expenses effectively.
The Importance of Yarn Count in the Spinning Process
In the textile industry, yarn count plays a crucial role in the spinning process. Different spinning methods, such as open-end spinning, ring spinning, air-jet spinning, and compact ring spinning, have specific requirements for yarn count. Each spinning method has optimal yarn count ranges to achieve the desired yarn characteristics.
When it comes to open-end spinning, which is known for its high production rates, the yarn count typically ranges from 20s to 40s. This method is commonly used for producing coarse and medium counts.
On the other hand, ring spinning is a traditional spinning technique that produces high-quality yarn. For ring spinning, the recommended yarn count ranges from 20s to 120s, depending on the desired fineness of the yarn.
Air-jet spinning, a process known for its high speed and efficiency, commonly uses yarn counts ranging from 6s to 30s. This method is suitable for manufacturing medium to coarse counts.
Compact ring spinning, a modern spinning technique that produces compact and stronger yarns, typically requires yarn counts from 30s to 160s. This method is ideal for producing fine and medium counts.
Understanding the relationship between yarn count and spinning processes is essential for textile manufacturers. By selecting the appropriate yarn count for each spinning method, manufacturers can achieve the desired yarn properties, such as strength, fineness, and evenness, which ultimately contribute to the quality of the final fabric.
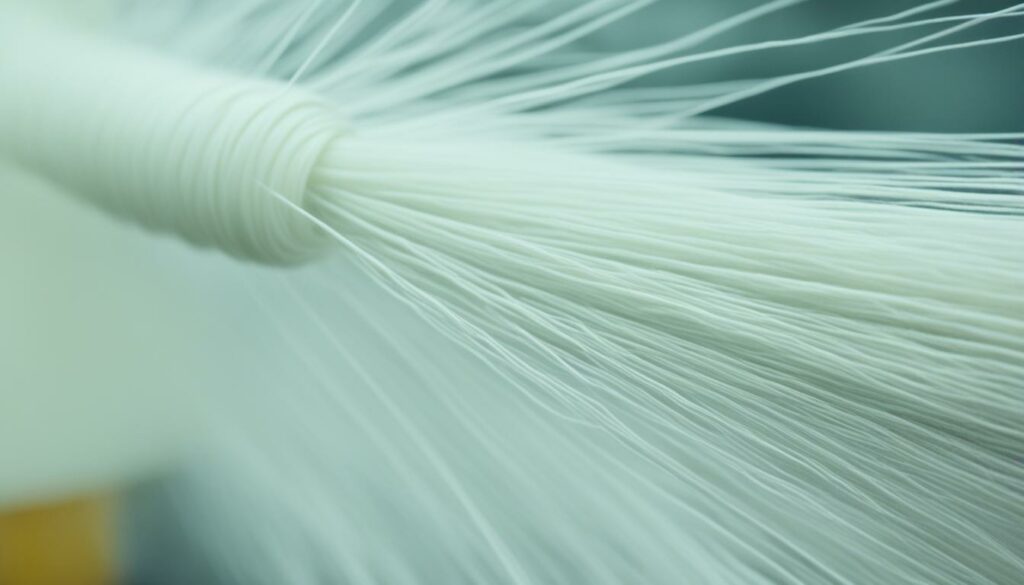
The Relationship Between Yarn Count and Spindle Types
Spinning Method | Optimal Yarn Count Range |
---|---|
Open-End Spinning | 20s to 40s |
Ring Spinning | 20s to 120s |
Air-Jet Spinning | 6s to 30s |
Compact Ring Spinning | 30s to 160s |
The Usage of Yarn Count in Different End Products
Yarn count plays a crucial role in determining the characteristics and performance of various end products. Different types of fabrics require specific yarn counts to achieve the desired qualities. Let’s explore how yarn count is used in different end products:
Yarn Count for Heavy Knits and Weaves
When it comes to heavy knits and weaves, higher yarn counts are often utilized. These fabrics require thicker yarns to increase their durability and strength. The use of heavier yarn counts ensures that the fabric can withstand the stress and strain typically associated with heavy-duty applications.
Yarn Count for Shirting Fabric
In the case of shirting fabric, medium to heavy yarn counts are commonly employed. These yarn counts strike a balance between fabric weight and comfort, resulting in high-quality shirting fabrics that are both durable and comfortable to wear. The use of medium to heavy yarn counts also enhances the fabric’s ability to retain its shape and resist wrinkling.
Yarn Count for Denim
Denim, a popular fabric in the fashion industry, requires medium to heavy yarn counts. The use of these yarn counts ensures that denim fabrics possess the necessary robustness and durability to withstand everyday wear and tear. Additionally, the use of medium to heavy yarn counts contributes to the distinctive texture and appearance that denim is known for.
Yarn Count for Towels
When it comes to towels, finer yarn counts are commonly utilized. This is because finer yarns result in a soft and absorbent texture, making them ideal for producing high-quality towels that offer superior drying capabilities. The use of finer yarn counts also enhances the overall plushness and comfort of the towels.
Yarn Count for Fine Weight Fabrics
In the case of fine weight fabrics, such as lightweight shirts or delicate garments, finer yarn counts are usually preferred. These yarn counts provide a delicate and lightweight texture, ensuring that the fabric drapes beautifully and offers a luxurious feel. Fine weight fabrics made with finer yarn counts are often favored for their breathability and smoothness against the skin.
By understanding the specific yarn count requirements for different end products, textile manufacturers can ensure that they produce fabrics that meet the desired characteristics and performance expectations. The selection of the appropriate yarn count is crucial in achieving the desired fabric qualities and ensuring customer satisfaction.
Yarn Count Parameters for Australian Cotton
Australian cotton is renowned for its high quality in the textile industry. It is a preferred choice for yarn production due to its desirable characteristics. To ensure optimal yarn production, specific yarn count parameters are set for Australian cotton, taking into account various factors such as fiber fineness, contamination levels, and specific end product requirements.
The yarn count ranges for Australian cotton vary based on the spinning system utilized. Different spinning systems require specific yarn counts to achieve the desired yarn characteristics. These parameters play a crucial role in determining the quality and properties of the resulting yarn.
A key advantage of Australian cotton is its low contamination levels, which contribute to the production of high-quality yarn. The low contamination ensures that the yarn is clean and free from impurities, resulting in a superior end product.
Australian cotton is commonly used in the production of medium to fine weight fabrics. The favorable properties of Australian cotton, combined with the appropriate yarn count, contribute to the creation of textiles with excellent drape, texture, and overall quality.
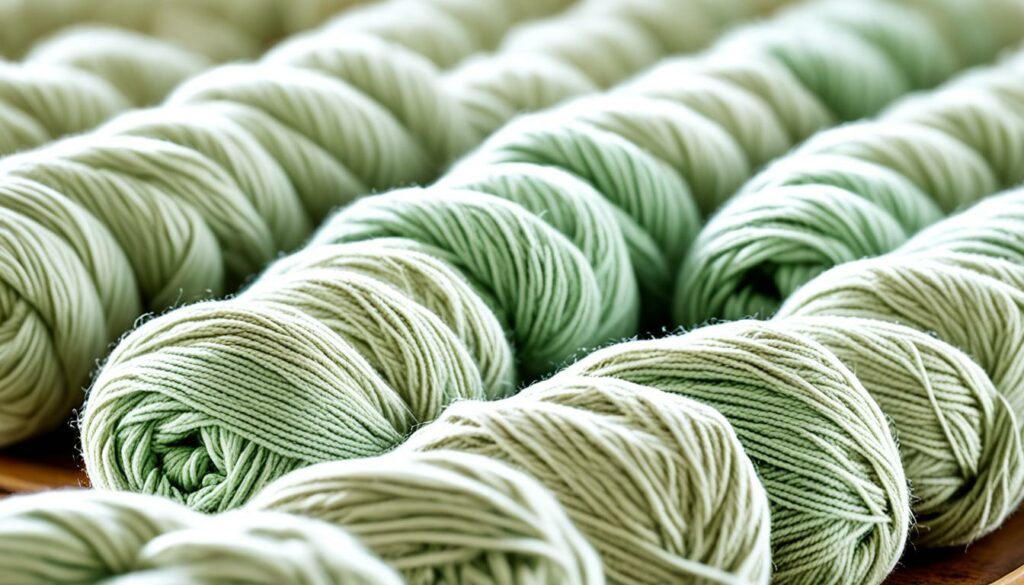
Spinning System | Yarn Count Range (Ne) |
---|---|
Open-end spinning | 10-24 Ne |
Ring spinning | 20-40 Ne |
Air-jet spinning | 12-30 Ne |
Compact ring spinning | 30-60 Ne |
The table above illustrates the typical yarn count ranges for different spinning systems used with Australian cotton. These ranges provide guidance for achieving the desired yarn count and ultimately, fabric characteristics.
Importance of Consistency in Yarn Count
Consistency in yarn count is essential for maintaining the quality and integrity of fabric production. Off-specification count variations can have detrimental effects on fabric weight, performance, and aesthetics. It is crucial to ensure acceptable count variations by implementing effective measures for measuring and monitoring yarn count.
By maintaining consistency in yarn count, we can prevent deviations from the desired fabric characteristics. Fabric weight variations can result in inconsistencies in garment sizing and fit, affecting the overall customer experience. Additionally, count variations can impact the strength and durability of the fabric, reducing its lifespan and compromising its performance.
Measuring count variations is typically achieved by weighing 100-meter lengths of yarn from multiple bobbins or packages. This process helps identify any discrepancies and ensures uniformity in the yarn count throughout the production process. Acceptable count variations are determined based on industry standards and specific fabric requirements.
Consistency in yarn count not only improves the overall quality of the fabric but also facilitates efficient production and reduces waste. By minimizing count variations, we can optimize the consumption of raw materials, ultimately enhancing sustainability in textile manufacturing.
Benefits of Consistency in Yarn Count:
- Ensures uniform fabric weight and performance
- Maintains desired fabric aesthetics
- Improves garment sizing and fit
- Enhances fabric strength and durability
- Optimizes raw material consumption
- Promotes sustainability in manufacturing
Quote:
“Consistency in yarn count is the key to achieving high-quality fabric that meets the desired specifications. By closely monitoring count variations and adhering to industry standards, we can ensure a uniform and superior end product.”
Acceptable Count Variations in Yarn
Fabric Type | Acceptable Count Variations |
---|---|
Heavy Knits and Weaves | ±5% |
Shirting Fabric | ±3% |
Denim | ±7% |
Towels | ±2% |
Fine Weight Fabrics | ±1% |
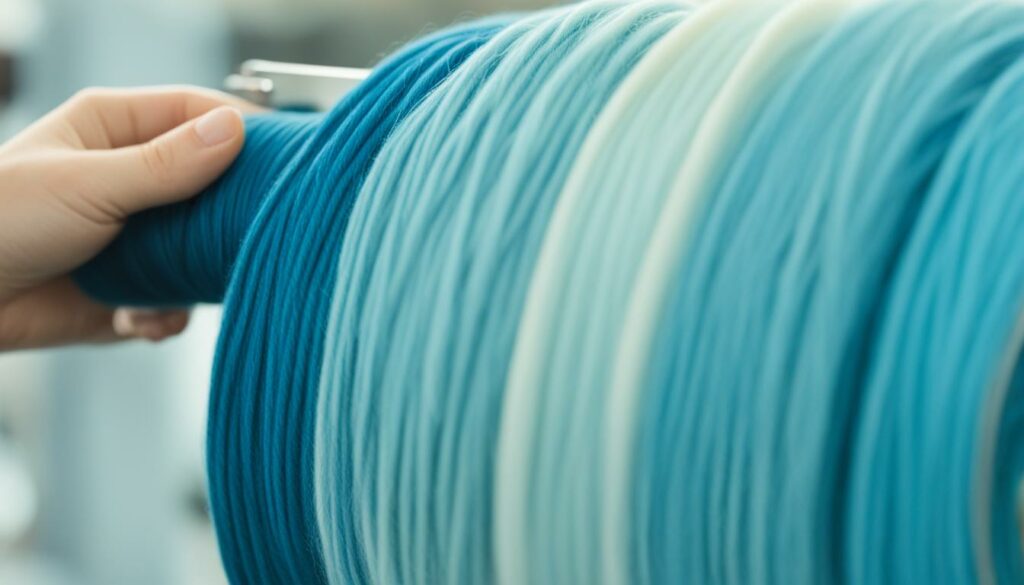
Different Measures of Yarn Count
When it comes to yarn count, there are various measures and systems used in the textile industry to determine the fineness and thickness of yarn. These measures provide valuable information that assists manufacturers in producing high-quality fabrics.
Direct System and Yarn Count
The direct system is one method used to measure yarn count. It involves determining the weight of a consistent length of yarn. Common units of measurement in the direct system include tex, decitex, and denier. These measurements indicate the weight of yarn in grams per a specific length, such as one kilometer or one meter.
Indirect System and Yarn Count
The indirect system is another approach to determine yarn count. It measures the length of a consistent weight of yarn. The most common measures in the indirect system are the English Cotton Count (Ne) and Metric Count (Nm). These measures indicate the number of hanks of yarn per pound or kilogram. The Ne value represents the number of 840-yard hanks per pound, while the Nm value indicates the number of 1000-meter hanks per kilogram.
Worsted Count
For specific types of yarn, such as worsted yarn, a distinct measure is used. The Worsted count indicates the number of hanks of yarn per pound, similar to the Ne value in the English Cotton Count. Worsted count is commonly used in the production of high-quality woolen fabrics.
These different measures of yarn count play a crucial role in the textile industry, providing valuable information about the fineness, thickness, and weight of yarn. By understanding and utilizing these measures, manufacturers can optimize their production processes and create fabrics that meet the desired quality and performance standards.
Conclusion
Summarizing the importance of yarn count in textile manufacturing, we understand that it plays a critical role in determining fabric characteristics, end-use applications, and production costs. Selecting the appropriate yarn count is essential for achieving desired fabric properties and aesthetics. The quality of yarn directly impacts the final fabric, making yarn count a crucial consideration for manufacturers.
By considering factors such as fiber type, end-use requirements, fabric structure, and aesthetic preferences, manufacturers can optimize their fabric production processes and create high-quality textiles. Yarn count acts as a key parameter that influences the weight, texture, and appearance of the fabric. It serves as a guide to achieve consistency and uniformity in yarn production, enabling manufacturers to meet the requirements of various end products.
As we conclude, it is evident that yarn count holds significant importance in the textile industry. Its impact on fabric properties, versatile applications, and influence on production costs cannot be overstated. By recognizing the significance of yarn count and employing it effectively, manufacturers can enhance the quality of their fabrics and stay ahead in the competitive textile market.